- مقدمه
فرآیند'>فرآیند شاو نوعی روش ریخته گری دقیق است که به وسیله آن می توان به راحتی قطعاتی با صافی سطح عالی و ابعاد دقیق تولید کرد. قالب ساخته شده به این روش حاوی اتیل سیلیکات مایع می باشد. در این روش جهت قالب گیری از اتیل سیلیکات نسوز به جای سیلیس استفاده می شود. در این صورت از بروز مشکلاتی که سیلیس ممکن است به وجود بیاورد جلوگیری می شود. یکی از ویژگیهای این روش این است که در فرآیند تولید قالب نیاز به پخت با دمای بالا (عملیات پخت) است و از طریق پخت در دمای بالا میتوان قالبهای خنثی تولید کرد که میتوان انواع آلیاژهای آهنی و غیرآهنی را به طور رضایتبخشی در آن ریختهگری کرد. تا قبل از حضور دستگاه های CNC این روش به عنوان یکی از معتبرترین روش های تولید قطعات صنعتی با دقت بالا شناخته می شد. دانشمندان قبل از جنگ جهانی دوم متوجه شدند که استر سیلیکون را توان به عنوان چسب برای مواد نسوز نظامی استفاده کرد. از آن زمان به بعد مانند سایر روش های ریخته گری، چسب مورد استفاده و روش تولید قالب به طور گسترده توسعه یافت. بر این اساس، درخواست های ثبت اختراع زیادی وجود داشت و بسیاری از اطلاعات فنی توسط پتنت روش ریخته گری شاو به ثبت رسید. زمانی که کیفیت یا دقت ابعادی و تولید قطعات ریخته گری با عیوب کمتر نیاز است، استفاده از این روش ریخته گری ایده خوبی به نظر می رسد. در این مقاله سعی شده است تا عوامل مختلف در تولید قالبها و قطعات جهت ریخته گری چدن به روش شاو بررسی شود. می خواهیم در مورد فرآیند تولید چسب، مواد نسوز و ساخت قالب و همچنین مهندسی فلزات و ابعاد ریختهگری بیشتر بدانیم. کیفیت محصولات تولید به این روش به دقت مورد بررسی قرار خواهد گرفت.
ماده قالب شامل پودر نسوز ریزدانه، چسب اتیل سیلیکات مایع، و ژل کننده است. انتخاب مواد نسوز خوب دو مزیت عمده به همراه دارد:
1) با استفاده از مواد نسوز با ذرات ریز می توان ریخته گری با سطح خوب تولید کرد.
2) با انتخاب یک ماده نسوز پایدار حرارتی، تغییرات غیرقابل پیش بینی در ابعاد قالب هنگام تماس فلز مذاب در حین ریخته گری و انقباض ایجاد شده در هنگام انجماد را می توان به طور دقیق تخمین زد.
دوغاب خوب مخلوط شده (slurry) با سیالیت خوب را درون قالب (جعبه قالب) بریزید. اگرچه زمان خودگیری بستگی به مقدار ژل کننده دارد، اما مواد قالب در مدت زمان کوتاهی به حالت ارتجاعی سفت می شود. سپس می توان مدل و قالب را از هم جدا کرد. در این مرحله می توان مزایای زیر را از این روش به دست آورد.
1) دوغاب مایع در اطراف مدل ریخته می شود تا از تماس جامد بین مدل و دوغاب اطمینان حاصل شود و بدین ترتیب می توان ریخته گری با ابعاد دقیق و شکل پیچیده به دست آورد.
2) مواد دوغاب در تماس با مدل سفت می شود و در نتیجه می توان مدل هایی از اشکال پیچیده را با دقت بازتولید کرد.
3) از آنجایی که قالب ژله ای حالت الاستیک دارد، در هنگام جدا کردن مدل، قالب دچار اعوجاج نمی شود و بنابراین حالت قالب به خوبی حفظ می شود.
4) به دلیل الاستیک بودن حتی اگر کمی شیب منفی هم در مدل وجود داشته باشد، باز هم قالب به راحتی از مدل جدا می شود.
5) مواد قالب جهت سفت شدن نیاز به حرارت دیدن ندارد. در نتیجه محدودیتی در انتخاب نوع مدل وجود ندارد.
پس از بیرون آوردن از مدل برای حذف الکل آزاد شده، قالب بلافاصله با مشعل گازی حرارت می بیند (فرایند شاو) یا با غوطه ور شدن در یک حمام تثبیت کننده تثبیت می شود و سپس به سرعت با یک مشعل گرم می شود (فرایند Unicast). هنگامی که در فرایند شاو با مشعل حرارت داده می شود، ترک های ریز روی سطح قالب و داخل مواد قالب ایجاد می شود. این ترک ها روی سطح ریخته گری تاثیری ندارند. فلز مذاب در شکافهای ریز فرو نمیرود، بلکه اجازه میدهد هوا یا گاز در طول ریختهگری خارج شود و در نتیجه تهویه را بهبود میبخشد. سپس قالب در کوره ای با دمای تقریباً 1000 درجه سانتیگراد پخته می شود. به این ترتیب مواد قابل احتراق در قالب با اطمینان حذف شده و قالبی پایدار با استحکام، سختی، پایداری و ابعاد دقیق ایجاد می شود. مراحل مختلف در تولید یک ریخته گری با استفاده از روش ریخته گری شاو در شکل نشان داده شده است.
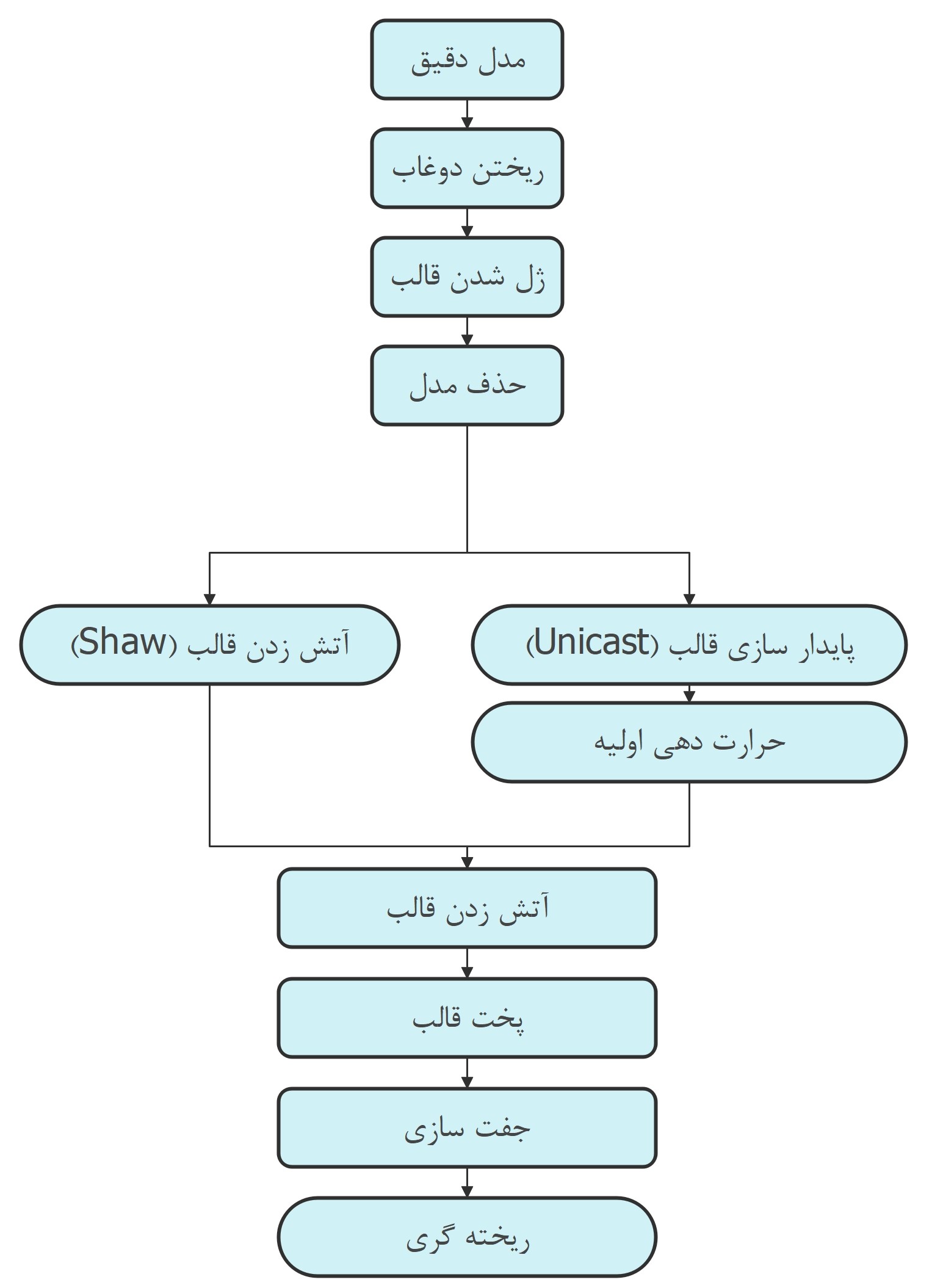
قالب های تولید شده به روش ریخته گری شاو دارای مزایای زیر هستند:
1) ویژگی های جداسازی خوب مدل:
قالب ژل شده الاستیک باقی می ماند و انعطاف پذیری خوبی دارد. بنابراین، هنگامی که به اشکال پیچیده نیاز است، مدل و قالب را می توان بدون آسیب رساندن به قالب جدا کرد.
2) ثبات ابعادی:
در طی ریختهگری پس از شلیک، میتوان ریختهگریهای دقیق با اشکال و ابعاد پیچیده در محدوده تحمل تولید کرد.
3) استحکام قالب:
به اندازه کافی قوی برای ریخته گری بدون استفاده از قالب. مدرک به اندازه کافی بزرگ است.
4) مقاومت در برابر فروپاشی قالب یا ترک خوردگی:
ساختار داخلی مواد منحصر به فرد قالب مقاومت در برابر شکست را بهبود می بخشد و تاثیر قالب را در هنگام کوچک شدن قالب کاهش می دهد.
5) مقاومت در برابر شوک حرارتی:
به دلیل ساختار داخلی منحصر به فرد مواد قالب، مواد قالب به راحتی منبسط می شود و در نتیجه می توان فلز مذاب را بدون حرارت دادن به قالب تزریق کرد.
6) مقاومت در برابر کنده شدن و شستشو:
از ورود ناخالصی ها به ذوب به دلیل استحکام پیوندهای سیلیس جلوگیری می کند.
7) پایداری و بی اثری:
از آنجایی که قالب پس از پخت خنثی است، تنها گازی که باید از مواد قالب خارج شود، گازی است که فضای قالب را اشغال می کند. با توجه به ساختار منحصر به فرد قالب، حفره ها به اندازه ای بزرگ است که اجازه دهد گاز به راحتی با حرکت درون قالب، خارج شود در حالی که فلز مذاب فضای قالب را پر کرده و به درون قالب نفوذ نمی کند.
- اتیل سیلیکات
اتیل سیلیکات یک اتصال دهنده سیلیس آلی بدون نمک های قلیایی است که مواد نسوز قالب را پیوند می دهد. اتیل سیلیکات از واکنش تتراکلرید سیلیکون و الکل اتیلیک به صورت رابطه زیر تولید می شود.
SiCl4 + 4C2H5OH à Si(OC2H5) + 4HCl
حذف اسید هیدروکلریک مهم است تا خاصیت ژل شدن در مرحله بعد به راحتی قابل تنظیم باشد. محصول واکنشی که هنگام استفاده از اتانول صنعتی حاوی آب به جای اتیل الکل خالص تولید می شود، مخلوطی از تترا اتوکسی سیلان و اتوکسی پلی سیلوکسان است. تترا اتوکسی سیلان حاوی تقریباً 28 درصد سیلیکا از نظر درصد وزنی است. از سوی دیگر، اتوکسی پلی سیلوکسان که به طور متوسط تا 5 اتم سیلیکون در یک مولکول دارد، حاوی 40 درصد سیلیس است. این محصول واکنش اتیل سیلیکات صنعتی نامیده می شود. و به دلیل داشتن محتوای سیلیس زیاد، معمولاً از آن استفاده می شود.
2-1- آبکافت
اتیل سیلیکات یک محلول پایدار و بدون قابلیت چسبندگی است. این محلول باید هیدرولیز شود. به این شکل که با آب واکنش داده و محلولی ایجاد می کند که شکلی از سیلیس را رسوب می دهد که خاصیت چسبندگی برای اتصال ذرات نسوز دارد. اتیل سیلیکات و آب با هم مخلوط نمی شوند مگر اینکه از حلالی مانند اتانول به عنوان حلال واسط برای حل هر دو استفاده شود. اتانول نیز برای رقیق کردن محلول به میزان سیلیس مورد نیاز عمل می کند. هیدرولیز می تواند توسط اسید یا باز رخ دهد. با این حال، سیلیس ژل شده توسط هیدرولیز توسط باز نسبتا سریع است. بنابراین، هیدرولیز توسط اسید بهتر خواهد بود. اسید سولفوریک یا اسید فسفریک اسیدهای مناسبی هستند، اما معمولاً از اسید کلریک استفاده می شود. محصولات هیدرولیز توسط اسیدها ماندگاری بسیار طولانی دارند و می توان آنها را به شکل اتیل سیلیکات هیدرولیز شده خریداری کرد که می تواند به راحتی بلافاصله در هنگام نیاز استفاده شود.
2-2- ژل سازی
برای اتصال ذرات نسوز، اتیل سیلیکات هیدرولیز شده باید ژل شود. ژل به دو صورت متصل می شود:
- پیوند خشک در هوا
3H4 Si04 à H2 Si2 O5 + H2 Si03 + 4H20
- پیوند ته نشینی
3H4 Si04 à 3Si02 gel + 6H20
در طول حرارت دادن، سیلیسیک اسید یا بایندر سیلیس متراکم می شود و سیمان سیلیکا نسوز را تشکیل می دهد. این سیلیس استحکام را در هنگام پخت به میزان قابل توجهی افزایش می دهد. روش های مختلفی برای رشد ژل اتیل سیلیکات هیدرولیز شده با اسید با استفاده از اصل هماهنگی زیر جلدی وجود دارد. اتیل سیلیکات هیدرولیز شده معمولاً با مقدار PH در محدوده 1.5 تا 3.0 تهیه می شود. در این محدوده، اتیل سیلیکات نسبتاً پایدار است و بالای 7.0 نیز پایدار خواهد بود. اما اتیل سیلیکات در PH بین 5.0 تا 7.0 نا پایدار است.
افزودن یک کاتالیزور بازی به محلول اتیل سیلیکات هیدرولیز شده می تواند مقدار PH را تا 5.0 افزایش دهد که در این مرحله محلول ناپایدار شده و ژل می شود. کاتالیزورهای بازی اصلی عبارتند از آمونیاک، نمک آمونیاک – استات ها، کربنات ها، هیدروکسید ها؛ یا نمک های آمونیاک آلی، پیپریدین، مورفولمار، تری اتیل امین و غیره. زمان واقعی ژل شدن بسته به نوع و مقدار ماده ژل کننده اضافه شده متفاوت است.
هنگامی که زمان پخت نیاز به کنترل دقیق دارد یا زمانی که شرایط نگهداری مهم است، از یک کاتالیزور ارگانیک استفاده می شود. این کاتالیزور باعث می شود که هیدرولیز و ژل شدن بدون اسید یا باز اتفاق بیفتد. عملیات حرارتی ویژه می تواند خواص پیوند را تغییر دهد و زمان ژل شدن را در هنگام افزودن آب بهبود بخشد.
- مواد نسوز
چندین ماده نسوز در ساخت قالب های شاو با استفاده از اتیل سیلیکات استفاده می شود. نمونه هایی از برخی از مواد نسوز در جدول زیر نشان داده شده است. برای انتخاب یک ماده مناسب برای یک هدف خاص، نکات زیر باید در نظر گرفته شود:
1) خلوص
2) مقاومت در برابر حرارت
3) پایداری
4) انبساط حرارتی
5) رسانایی توزیع حرارتی
6) اندازه ذرات
7) قیمت
نام ماده نسوز | فرمول شیمیایی | دمای ذوب درجه سانتیگراد |
منیزیم اکسید | MgO | 2،800 |
زیرکونیا | ZrO2 | 2،677 |
کلسیم اکسید | CaO | 2،600 |
زیرکون | ZrO2 . SiO2 | 2،420 |
زیرکونات کلسیم | CaO . ZrO2 | 2،345 |
منیزیم اسپینل | MgO . AlO3 | 2،135 |
آلومینا | Al2O3 | 2،015 |
مولایت | 3Al2O3 . 2Sio2 | 1،830 |
فیوزد سیلیکا | SiO2 | 1،723 |
ماده نسوز باید مقاومت کافی در برابر حرارت داشته باشد تا در برابر دمای ذوب ریزی فلز مذاب یا نرم شدن آن در دمای بالا مقاومت کند. در واقع، اگر ماده دیرگداز حاوی مقادیر کمی نمک فلزات قلیایی یا اکسیدهای آهن باشد، نقطه ذوب ماده نسوز به میزان قابل توجهی کاهش می یابد، بنابراین اگر ماده خالص باشد، نقطه ذوب معیار خوبی برای سنجش نسوز است. ماده نسوز انتخاب شده باید از پایداری بالایی برخوردار باشد. به عبارت دیگر نباید به راحتی باعث واکنش هیدراسیون یا واکنش با سایر مواد موجود در قالب یا فلز مذاب شود. پایداری حرارتی نیز مهم است چون انبساط حرارتی ناگزیر رخ می دهد. با این حال، تا زمانی که بتوان انبساط حرارتی را پیشبینی کرد، یعنی اگر ثابت و تکرارپذیر باشد، میتوان آن را به طور کامل پیشبینی کرده و میزان انقباض در نظر گرفت.
هدایت حرارتی یکی از ویژگی های ماده نسوز می باشد. هنگامی که یک قالب خاص و متخلخل می سازیم اندازه ذرات و توزیع آن در هدایت گرمایی مؤثر است. هدایت حرارتی بر سرعت انجماد و انتقال حرارت از طریق قالب و در نتیجه ساختار انجماد فلز تأثیر می گذارد.
قیمت نیز متغیر مهمی در انتخاب مواد نسوز است. قیمت به عوامل متعددی مانند در دسترس بودن، خلوص و نیاز اندازه ذرات بستگی دارد.
3-1- مواد قالب
اغراق نیست اگر بگوییم که کلید اصلی ساخت یک قالب خوب و تولید قطعات ریخته گری با کیفیت بالا به نحوه اختلاط مواد قالب گیری بستگی دارد. به منظور تولید حفظ کیفیت قالب، کنترل کیفیت مواد قالب با میزان مناسب بایندر و مقدار عامل ژل ساز ضروری است. در روش ریخته گری شاو تولید دوغاب با غلظت مناسب اهمیت بالایی دارد. اگر غلظت آن خیلی کم باشد، در هنگام پخت به راحتی در قالب ترک ایجاد می شود و اگر غلظت خیلی زیاد باشد، پر کردن قالب مشکل است.
هنگام انتخاب کیفیت مواد نسوز برای تولید قالب، می توان از اصول اعمال شده در ساخت قالب های ماسه ای به عنوان معیار استفاده کرد. استفاده از ماده ای با اندازه ذرات ریزتر دمای سطح را بهبود می بخشد. با این حال، نفوذپذیری هوا کاهش می یابد و در نتیجه گاز زدای بیشتری نیاز خواهد بود. در مورد استحکام، همانطور که انجمن ریخته گری آمریکا (AFS) اندازه گیری استحکام فشاری و کششی را اندازه گیری کرده، بسته به گرید انتخاب شده میزان استحکام نیز متفاوت خواهد بود. یکی از راه های بهبود استحکام افزودن ذرات نسوز درشت تر به پودر سرامیک است. در این حالت ذرات مختلف با اندازه های مختلف مخلوط می شوند تا ذرات ریز بتوانند فضای بین ذرات درشت را پر کنند. استحکام مخلوط مولایت پیوند یافته با اتیل سیلیکات در جدول زیر آورده شده است. همچنین مقاومت در برابر دما در شرایطی که ذرات ریز و درشت باهم مخلوط می شود آورده شده است. در این صورت با مخلوط ماسه و پودر، استحکام به حداکثر می رسد و این راه اقتصادی ترین روش استفاده از بایندر می باشد. مشخصات مخلوط به الزامات نظری و عملی بستگی دارد. در این زمینه لازم است برای کسب اطلاعات بیشتر به کتب مرجع در زمینه سرامیک مراجعه شود.
مواد نسوز اندازه ذرات | میزان مداد نسوز (cc/kg) | استحکام کششی (×10-3kgf/m3) |
قبل پخت | بعد پخت در دمای 1000 درجه |
هوا خشک | گرم کردن با مشعل | هوا خشک | گرم کردن با مشعل |
100 درصد مش 300 مولایت | 456 | - | 1.40 | - | 3.93 |
422 | - | 1.90 | - | 4.21 |
400 | 3.72 | 1.90 | 14.75 | 3.72 |
356 | - | 2.11 | - | 5.13 |
333 | 6.53 | 2.25 | 25.98 | 5.83 |
311 | - | 2.39 | - | 7.72 |
267 | 8.43 | 2.81 | 41.08 | 11.09 |
30% مش 16/30 30% مش 16/30 40% مش 300 | 267 | - | 6.32 | - | 11.73 |
222 | - | 7.51 | - | 15.94 |
178 | - | 8.29 | - | 19.87 |
4- ریخته گری فلز
از آنجایی که مزیت اصلی این روش قالبگیری این است که میتواند به طور مداوم ریختهگریهایی را تولید کند که تلورانسهای ابعادی دقیق دارند، بسیار مهم است که تجهیزات مونتاژ مدل و قالب با دقت بالایی ساخته شوند.
4-1- نحوه انجام کار
نمی توان قطعات ریخته گری را با جزئیات و دقت بیشتر نسبت به مدل تولید کرد. بنابراین دقت مدل بسار حائز اهمیت بوده و باید به دقت مونتاژ و کیفیت مدل توجه شود. در روش ریخته گری شاو از مدل دائمی برای قالب گیری استفاده می شود و در تئوری می توان از مواد مختلفی استفاده نمود. از انواع مواد مورد استفاده برای مدل ریخته گری به عنوان مثال می توان به چوب، گچ، گرافیت، رزین اپوکسی و فلز اشاره کرد. با این حال، در واقعیت، به دلیل اینکه دقت ابعادی مورد نیاز است، دامنه انتخاب ها محدود می شود. در مورد قالب های چوبی، آنها تحت تاثیر حرارت یا رطوبت هستند، بنابراین ابعاد می تواند تا 3٪ تغییر کند که به شدت بر دقت ابعاد محصول تأثیر می گذارد. در صورت استفاده از رزین پلیمری، خطر قابل توجهی وجود دارد. اعوجاج . ایجاد رینگ آسان است. برای به دست آوردن ابعاد دقیق، توصیه می شود از یک قالب خوب صیقلی استفاده شود و آلیاژ آلومینیوم به ویژه مناسب است. برای جداسازی بهتر مدل از قالب می توان از جدا کننده ها استفاده نمود. به عنوان مثال، از محلول بنزن حاوی 10% موم پیرافین یا محصولی با خواص مشابه استفاده می شود. جهت بستن درزها و جلوگیری از نشت دوغاب میتوان از وازلین استفاده نمود. حتی در مواردی که فیلت نیاز است با روغن های جامد می توان با روغن جامد این فیلت ها را ایجاد کرد. اگر به مقدار مناسب بمالید و خوب پاک کنید، برای خارج کردن مدل از قالب مشکلی پیش نمی آید. اما بهترین گزینه استفاده از اسپری سیلیکون یا همان اسپری جدا کننده قالب می باشد.
4-2 انواع قالب های شاو
قالبهای شاو را میتوان به روشهای مختلفی ساخت. برای نمونه، پوسته سرامیکی برای ساخت قطعات بزرگ و قالب یکپارچه بدون استفاده از لایه پشت قالب برای ساخت قطعات ریختهگری کوچک مناسب است. زمانی که قالب یا محصولی که قرار است ساخته شود بسیار بزرگ است، بهتر است با ساخت قالب دو لایه، هزینه تولید قالب کاهش یابد. در این حالت لایه اول به روش شاو ساخته می شود. برای پشت قالب به عنوان پشتیبان ارزان قیمت لایه اول، از چسب سیلیکات سدیم و ماسه معمولی استفاده می شود. برای تولید انبوه، فرآیند تولید قالب را می توان خودکار کرد تا قالب های زیادی تولید شود. برای تولید قالب دو لایه به دو مدل نیاز است. در صورتی که بخواهیم لایه پشتیبان در قالب ایجاد کنیم، نیاز به مدلی بزرگتر از مدل اصلی می باشد. پشت قالب پس از قالب گیری با مدل دقیق مونتاژ می شود و دوغاب سیال در فضای خالی بین قالب پشتیبان و مدل ریخته می شود.
اگر تیراژ پایین باشد، برای ساخت قالب پشتیبان نیازی به مدل دائمی نیست. مدل پشتیبان را می توان با پوشاندن مدل اصلی به ضخامت معین با موادی مانند ماسه روغنی، موم، نمد و ... بدست آورد که می تواند یک قالب پشتیبان بزرگ تولید کند.
4-3- کنترل کیفیت قالب
هنگامی که مدل از قالب خارج می شود، باید طی چندین مرحله روی آن کار شود که می تواند به طور قابل توجهی بر کیفیت قالب نهایی تأثیر بگذارد. در روش ریختهگری شاو، اثر ترکهای ریز تشکیل شده در مواد قالب تنها زمانی قابل حل است که مدل بلافاصله پس از برداشتن سوزانده شود. وقتی مواد قالبگیری برای مدت زمان قابلتوجهی در هوا خشک شود، ترکهای میکروسکوپی ایجاد نمیشوند. افزایش استحکام با پخت برای مواد خشک شده در هوا بسیار بیشتر است. با این حال، هنگامی که در هوای آزاد قرار می گیرد، ویژگی های تهویه، ذخیره سازی و تخریب در اثر شوک های حرارتی بدتر می شود (جدول 2 را ببینید).
ترک های درشت در گوشه های داخلی حفره قالب می تواند مشکل ساز باشد. برای اکثر طرح های ریخته گری، لبه های تیز مناسب نیستند. همچنین توصیه می شود که شعاع منحنی در گوشه ها 3 میلی متر یا بیشتر باشد. الکل تبخیر شده به راحتی می سوزد. با این حال، سوختن با افزایش میزان شعله گاز تقویت میشود. بهتر است قالب بر روی یک شبکه توری قرار گیرد تا عبور هوا در طول احتراق تسهیل شود.
یک روش ریختهگری پیشرفتهتر، فرآیند Uni-Cast است که در آن قالب جدا شده به سرعت با یک مشعل حرارت داده میشود و قبل از پخت در یک حمام مایع برای تثبیت غوطهور میشود. به عنوان مثال با تثبیت از طریق خیساندن آن در حمام الکل اتانول یا متاتول به مدت حدود یک ساعت ، پایداری و استحکام ابعاد قالب بهبود مییابد. وقتی قالب کوچک باشد با قرار دادن آن در یک کیسه پلاستیکی در بسته، تثبیت می شود.
پس از گرم شدن سریع قالب با مشعل، به دو دلیل زیر آتش زده می شود.
1) برای به دست آوردن یک قالب بی اثر با سوزاندن مواد آلی باقیمانده و حذف رطوبت.
2) به منظور بهبود استحکام قالب با پی بردن به اثر
محدوده قابل توجهی از دمای پخت در مقالات پیشنهاد شده است، از 300 تا 1300 درجه سانتیگراد. در حالی که اولین دمای هدف را می توان با تف جوشی در 500 درجه سانتیگراد به دست آورد، پخت در دمای کمتر از 1000 درجه سانتیگراد عملاً به طور قابل توجهی استحکام را بهبود نمی بخشد. یک جو کمی اکسید کننده هنگام پختن قالب برای تقویت احتراق مواد فرار باقیمانده مناسب است. قالب های کامپوزیتی با تشعشع در یک کوره تونلی ساخته می شوند تا سطح سرامیک را بدون گرم کردن بیش از حد قالب پشتیبان گرم کنند.
دمای پیش گرم قالب بسته به ضخامت سطح مقطع محصول و نیازهای مربوط به خواص مواد متفاوت است. ذوب در حالی که قالب کاملاً خنک نشده است درون قالب ریخته می شود. هنگامی که از قالب استفاده نمی شود، مونتاژ یک قالب جزئی را می توان با نصب پین های مونتاژ قالب در طول فرآیند ساخت مدل تسهیل کرد. درزهای قالب با اعمال درزگیر مناسب آب بندی می شود. با این وجود کیفیت ریخته گری در خط جدایش قالب کمتر است. قبل از ریخته گری، یک جسم سنگین را روی قالب قرار دهید یا آن را با یک تسمه فلزی ببندید.
5- کنترل کیفیت قطعه نهایی
سنجش کیفیت ریخته گری دقیق به سه عامل زیر بستگی دارد:
1) دقت ابعاد
2) سطح و ظاهر
3) وجود نقص
5-1 دقت ابعاد
دقت ابعاد محصول با دقت مدل تعیین می شود و همچنین بستگی به دقت مونتاژ قالب های جزئی دارد. طبیعی است که تلورانس های ابعادی داخل قالب نسبت به اتصالات قالب بیشتر است. مواد قالب گیری نیز بر خواص حرارتی و دقت ابعادی مواد تأثیر می گذارد. هر دوی این عوامل ارتباط نزدیکی با دمای فلز مذاب دارند و دمای فلز مذاب تأثیر عمده ای بر دقت ابعاد دارد. با ننظارت دقیق بر فرآیند ذوب ریزی می توان تاثیر آن را کاهش داد. برای تولید پایدار، توصیه می شود قطعاتی که بعداً مونتاژ می شوند با همان ذوب تولید شوند.
ابعاد معمولی ریخته گری های فولادی تولید شده به روش ریخته گری شاو
مقادیر مجاز به شرح زیر است:
برای ابعاد 25 میلی متر یا کمتر دقت در محدوده 0.08± میلی متر
برای ابعاد 25 تا 75 میلی متر دقت در محدوده 0.13± میلی متر
برای ابعاد 75 تا 200 میلی متر دقت در محدوده 0.38± میلی متر
برای ابعاد 200 تا 375 میلی متر دقت در محدوده 0.76± میلی متر
برای ابعاد بالاتر از 375 میلی متر در محدوده 1.4± میلی متر
در محل های نزدیک خط جدایش به میزان 0.25± تا 0.5± میلی متر به این مقادیر اضافه می شود.
5-2 جلو بیرون
دمای سطح ریخته گری های تولید شده به روش ریخته گری شاو بسته به عوامل مختلفی از جمله کیفیت نسوز، دمای فلز مذاب و قالب و واکنش بین فلز مذاب و قالب متفاوت است. هرچه ذرات نسوز استفاده شده ریزتر باشد، دمای سطح بهتر است. اگر قالب از قبل گرم شده باشد و دمای ریختن بالا باشد، کیفیت سطح بدتر می شود. در مورد فولاد ریخته گری، زبری سطح حدود 2μm cla است. و برای آلیاژهای غیر آهنی می توان به مقادیری بهتر از این دست یافت. همچنین، در مورد محصولات ریخته گری شن و ماسه حدود 5~10μm cla است.
سطوح به شدت اکسید شده نه تنها دقت ابعادی بلکه کیفیت سطح را نیز به طور مستقیم و غیرمستقیم از طریق نیاز به شات بلاست بدتر می کند. به منظور کاهش این اثر اکسیداسیون، ممکن است از یک اتمسفر گاز بی اثر استفاده شود.
5-3 رفع مشکل حفره های گازی
ریختهگری شاو به دلیل سمی بودن مواد قالبگیری، نسبت به سایر روشهای ریختهگری سرعت سرد شدن فلز نسبتاً پایینتر است. بر این اساس، ساختار میکروسکوپی درشت است و ممکن است بسته به هدف، این روش قابل اجرا نباشد. این مشکل را می توان با تغییر دانه بندی مواد قالب حل کرد. خنک شدن آهسته ممکن است تا حدی به دلیل کربن زدایی یا اکسیداسیون سطحی در فولاد ریختگی باشد. در مورد فولاد ریختهگری شده حاوی کربن، سطح ممکن است تحت تأثیر حفرهها قرار گیرد.
کربن زدایی بسته به اینکه ریخته گری در دمای بالای 870 درجه سانتیگراد نگهداری شود رخ می دهد. در واقع مشکل کربن زدایی را می توان به روش زیر حل کرد. هنگامی که قالب در یک ظرف قرار می گیرد، هگزا متیلن تترامین به سطح بیرونی فلز، در یک اتمسفر احیا کننده اعمال می شود، یا قالب را خلاء می کنند تا هوا از قالب خارج شود و با گاز بی اثر پر شود. به طور موثر نشان داده شده است که پدیده حفره ای شدن با دفع گرما از سطح (temperature desorption) مرتبط است که این دو پدیده به دلیل تشکیل مونوکسید کربن است. با اتمسفر درون فلز مذاب و با اکسیژن آزاد شده از سیلیس که به عنوان یک اتصال دهنده در قالب عمل می کند واکنش نشان می دهد. بنابراین، کربن زدایی رخ می دهد و حباب های مونوکسید کربن ایجاد می شود که باعث ایجاد حفره در سطح ریخته گری می شود. از آنجایی که اکسیژن همیشه در سیلیس وجود دارد که به عنوان یک عامل جمع کننده عمل می کند، حذف کامل پدیده کربن زدایی غیرممکن خواهد بود. پیشنهاد شده است که خواص سطحی ریختگی ممکن است با تامین گاز از طریق داخل مواد قالب در طول خنک شدن ریختگی تغییر کند. سطح را می توان با استفاده از آمونیاک نیترید کرد و با استفاده از تولید کربن می توان سوزن ها را روی سطح ایجاد کرد.
منبع: مقاله کره ای به عنوان فرآیند شاو نوشته شده توسط پرفسور هیووک کوون استاد مهندسی در دانشگاه یونگنام
انتقال حرارت در ریخته گری دقیق...
ما را در سایت انتقال حرارت در ریخته گری دقیق دنبال می کنید
برچسب : نویسنده : shaw-process بازدید : 3 تاريخ : شنبه 1 ارديبهشت 1403 ساعت: 21:02