پمپ یکی از مهم ترین اجزای مورد استفاده در صنعت می باشد. پمپ های گریز از مرکز بیشترین کاربرد را در بین پمپ های صنعتی دارد. دغدغه اصلی پمپ سازان در ساخت پمپ ها، افزایش هر چه بیشتر بازدهی پمپ می باشد. مهم ترین قطعه به کار رفته در پمپ ها پروانه آن می باشد. در واقع می توان قلب پمپ را پروانه آن در نظر گرفت. جهت افزایش بهره وری پمپ، هرچه دقت ابعادی و صافی سطح پروانه بهتر باشد، بازدهی پمپ بالاتر خواهد بود. معمول ترین روش تولید پروانه پمپ، ریخته گری است. جهت افزایش دقت ساخت پروانه پمپ، از روش های ریخته گری دقیق استفاده می شود. در این صورت بازدهی پمپ 3 تا 7 درصد افزایش خواهد داشت. معمولا با ساخت مدل مومی و ساخت قالب سرامیکی پوسته ای به روش Invetment اقدام به ساخت قالب ریخته گری دقیق جهت ریخته گری پروانه می کنند. در این روش کیفیت خوبی خواهیم داشت اما معایبی نیز داردکه در ادامه بیان می شود:
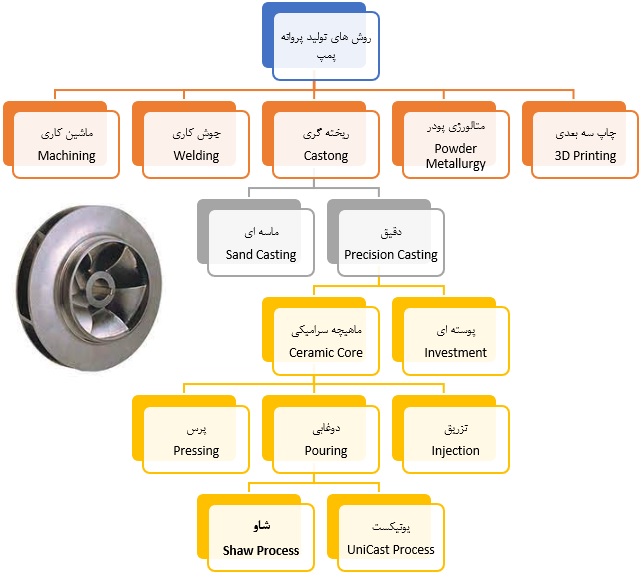
در روش ریخته گری لایه نشانی سرامیکی با مدل مومی به تجهزات زیادی مورد نیاز است. تجهیزاتی از قبیل دستگاه تزریق موم، پاتیل دوغاب سرامیکی، دستگاه ماسه پاش، دستگاه موم زدا، تجهیزات مربوط به خارج کردن قطعه از قالب سرامیکی و... .
- بالا بودن هزینه مواد مصرفی
برای لایه نشانی سرامیک، می بایست دوغاب سرامیکی درست کرده و درختچه مومی را درون آن غوطه ور کنیم. در صورتی که ظرفیت تولید کم باشد، دوغاب ساخته شده به مرور زمان فاسد می شود و دیگر قابلیت استفاده ندارد. حال اگر قطعه بزرگ باشد، نیاز به پاتیل بزرگتر و دوغاب بیشتر است.
- بالا بودن ساخت قالب تزریق موم
ساخت قالب تزریق موم بسیار گران است و برای تعداد کم به صرفه نیست. قالب تزریق حتما می بایست فلزی باشد. در مواردی از چاپ سه بعدی استفاده می کنند. با این وجود مدل ساخته شده بعد از ذوب ریزی از بین می رود و قابلیت استفاده مجدد را نخواهد داشت. در این صورت قیمت تمام شده قطعه نیز افزایش خواهد یافت.
مراحل این روش بسیار زیاد است. با توجه به اینکه دوغاب سرامیکی به صورت لایه لایه روی مدل مومی می نشیند، برای خشک شدن هر لایه می بایست زمان زیادی صرف نمود. فقط ساخت پوسته سرامیکی با استحکام کافی در حدود 10 تا 20 روز زمان می برد. مگر از دوغاب های خاصی استفاده شود که آن هم پر هزینه است. تازه این فقط بخشی از فرآیند است.
با توجه به زمان بر بودن فرآیند به ناچار نیروی کار بیشتری نیاز است. در صورتی که قطعه بزرگ باشد، علاوه بر افزایش هزینه تجهیزات، نیروی انسانی هم توان لایه نشانی درختچه مومی را ندارد که مجبور خواهیم بود از بازوی رباتیک استفاده کنیم.
در ریخته گری دقیق با مدل مومی محدودیت وزن و ابعاد خواهیم داشت. این روش برای قطعات کوچک با تیراژ بالا مناسب است اما در صورتی که قطعه بزرگ باشد دیگر امکان لایه نشانی سرامیکی نخواهد بود.
با توجه به موارد گفته شده پروانه تولید شده به روش Investment بسیار پرهزینه و زمان بر است. بسیاری از پمپ سازان عطای ریخته گری دقیق را به لقای آن می بخشند. اما روش دیگری نیز وجود دارد. ماهیچه سرامیکی به راحتی درون قالب ماسه ای قرار گرفته و سطح درونی قطعه را بهبود می بخشد. امکان ماشین کاری سطح بیرونی پروانه نیز به راحتی فراهم است. تولید پروانه به این روش معایب گفته شده در بالا را پوشش می دهد. روش های مختلفی برای تولید ماهیچه سرامیکی وجود دارد. به انواع روش های قالب گیری سرامیکی می توان ماهیچه را تولید کرد که شامل پرس تزریق و ثقلی می باشد. عمده ترین روش مورد استفاده برای تولید ماهیچه سرامیکی، قالب گیری تزریقی می باشد. این روش بیشتر برای پره های توربین مورد استفاده قرار می گیرد. این روش نیز مانند روش موم فنا شونده دارای معایبی می باشد. در این روش نیاز به دستگاه تزریق سرامیک می باشد. چسب مومی می بایست با پودر سرامیک به صورت خمیری شده و به داخل قالب تزریق شود. دستگاه تزریق و ساخت قالب گران قیمت است.
بهترین روش جهت ریخته گری دقیق پروانه ریخته گری به روش شاو می باشد. در این روش پودر سرامیک با چسب پلیمری و هاردنر ترکیب شده و به صورت دوغابی درون قالب ریخته می شود. پس از چند دقیقه سرامیک ریخته شده درون قالب به صورت ژل خالص در می آید. ژل سرامیک به راحتی از قالب بیرون می آید. سپس ژل سرامیک آتش زده شده و پخته می شود. در روش شاو این قابلیت وجود دارد که قالب و ماهیچه پیش گرم شوند. در این صورت مقاطع نازک به راحتی پر خواهد شد. در انتخاب مدل ریخته گری نیز محدودیتی وجود ندارد. در این روش علاوه بر عدم وجود مشکلات ریخته گری با موم فنا شونده که در بالا بیان شد، دارای مزایایی است که در ادامه بیان خواهد شد.
از آنجایی که به صورت دوغابی درون قالب ریخته شده و قالب هیچ حرارتی نمی بیند از مواد مختلف می توان برای قالب گیری استفاده نمود. موادی از قبیل آلومینیوم، فولاد، رزین، موم، چوب، گچ و... .
با توجه به میزان هاردنر در کمتر از چند دقیقه پس از ریختن سرامیک درون قالب امکان خارج کردن آن پس از ژل شدن وجود دارد. به جرعت می توان گفت سریع ترین زمان برای قالب گیری چه ماسه ای و چه سرامیکی این روش می باشد.
- امکان پیش گرم قالب و ماهیچه
این روش تنها روش ریخته گری دقیقی است که هم می توان پیش گرم کرد و هم بدون پیش گرم می توان ذوب ریزی را انجام داد.
- امکان قالب گیری با مدل و جعبه ماهیچه ماسه ای
در اکثر موارد قالب و جعبه ماهیچه ریخته گری ماسه ای وجود دارد. در این روش به راحتی از همان قالب ها می توان استفاده نمود و به ریخته گری دقیق دست یافت.
- خارج کردن راحت تر سرامیک از درون قالب
با توجه به خاصیت ارتجاعی و لاستیک مانند سرامیک ژله ای، امکان خارج کردن آن حتی در صورتی که مقدار کمی شیب منفی در قالب باشد نیز وجود دارد.
بنابراین ساخت پروانه پمپ به روش ریخته گری شاو بهترین گزینه است. هم از نظر زمان و هم از نظر هزینه به صرفه خواهد بود.
+ نوشته شده در پنجشنبه ۱۴ دی ۱۴۰۲ ساعت 10:37 توسط میرسیدی |
انتقال حرارت در ریخته گری دقیق...
ما را در سایت انتقال حرارت در ریخته گری دقیق دنبال می کنید
برچسب : نویسنده : shaw-process بازدید : 11 تاريخ : يکشنبه 8 بهمن 1402 ساعت: 15:12